Customer Story: There’s No Second Chances When Installing Steel Beams
How Studio Steel Uses Cintoo to Install Successfully on the First Go
Evo DC is the Construction Tech support for Studio Steel which is primarily a metal fabrication business specialising in structural steel and customised metal works.
Clint Stevens
BIM Coordinator, Evolution Digital Construction
How Studio Steel Uses Cintoo to Install Successfully on the First Go
“Our goal is to solve problems before they occur,” says Clint Stevens, BIM Coordinator at Evolution Digital Construction part of the Evolution Industries Group. Evo DC is the Construction Tech support for Studio Steel which is primarily a metal fabrication business specialising in structural steel and customised metal works. Evolution industries Group is born out of a necessity to control the supply chain on their projects from engagement in early design through to hand over and covers abrasive blasting & protective coatings and crane, scissor lift & equipment hire internal processing and our professional in-house team of installers “Cintoo has helped us detect problems before they occur and by creating visual reports, we can communicate to others with clarity and all the context needed to make decisions.”

Models of steel beams to be implemented.
Studio Steel operates in highly complex situations installing a wide range of projects in all kinds of environments, such as New Build, Renovations, Retro fit upgrades and architectural feature works. Precision becomes the nature of Studio Steel’s work, dependent upon having the right understanding of a site’s conditions before any steel is produced and site teams mobilised for installation. Studio Steel’s passion for the job with all its complexities and their commitment to building better and smarter is what makes their business stand out from others.
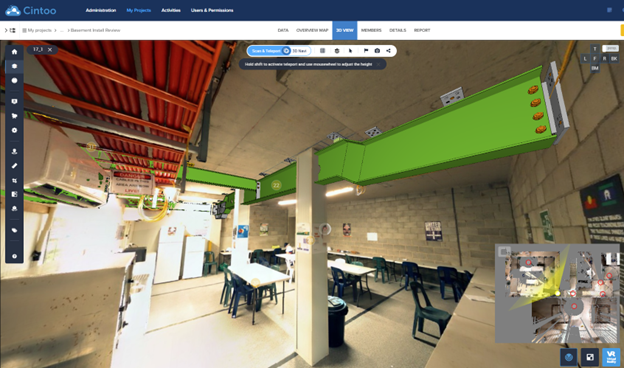
The model as seen overlayed to the as-built conditions on Cintoo.
How Do You Manage a 900-kilo Beam Installation Around Services During Planned Shut Downs?
In a recent project, Clint’s team was tasked with installing 50+ 900kg beams. A feat on its own, however, some beams were required to be installed through an electrical grid in the basement of an active amenities block. “There were no second chances,” Clint says. “Our client had commitments to keep the amenities active during operation hours and we had an 8hr fixed shut down window to operate in including the demolition by others to provide the access paths for this install”. Planning accordingly became Studio Steel’s objective to be as precise as possible, and Cintoo helped with the coordination of models and accurate clash detection to ensure the first install was the only install needed and all services and demolition plans were known to secondary contractors on arrival to complete their roles.
Studio Steel is a BuildingPoint (UPG) -backed business, meaning all geospatial solutions (including data collection) is built upon Trimble equipment and software solutions. Clint says his team first ascertains the as-built conditions of a site using Trimble laser scanning and survey equipment. “We want to get that laser scan data out in front of people like draftsmen and installers to be able to plan accordingly,” Clint says. “Often times, as-built information from documentation isn’t always accurate, and we need the most accurate data to perform installation reviews.” By optimising the planning part of a construction project, Studio Steel can better organise all different team members around a single visual source of truth and overlay their accurate CAD models of the new install. This service helps Clint’s team deliver the best product to their clients working through all the potential risk areas in a virtual environment before bringing it to the live environment.

The steelwork visualized.
How Does Cintoo Help With Clash Detection?
Part of this process relies on Cintoo’s ability to convert laser scan data at the same resolution as the source scanner in one easy-to-use, web-based browser. “We want to plan and structure access,” Clint describes. “What that means is, even if someone doesn’t know what a point cloud is, we can have a conversation around clash detection and instability.”
One of Studio Steel’s recurrent achievements for clients is their ability to detect clashes early and get the right installation procedures planned resulting in a faster time to install with increased awareness around the site environment altogether increasing the safety of their team’s involvement. “We need to know where the steel’s going and how so we can open up Cintoo on a video conference to view the whole site and have walkthroughs with others. We become more prepared, even for things like moving in a crane to do a truck unload. We know where that’s going to happen and how when access is limited,” Clint says.
Studio Steel is also able to detect site conditions early on, which ups their level of precision and safety even more. For instance, Clint’s team can quickly capture and display the most recent site conditions which helps them structure their services from end to end, like confirming the site is ready to receive the steel before they mobilise a team. Cintoo provides the platform for collaboration.

Detecting conditions based on as-built conditions, Studio Steel is able to posture steel more effectively.
How Studio Steel Offers a Better Service to their Clients
In another project Studio Steel was involved in, their team was responsible to install a new steel structure on a concrete slab prepared by others. During setout it was apparent some of the build was not as documented and areas of it incomplete and Cintoo became their reporting tool to inform the client that the site was not ready to receive the steel work and that modifications would be required should the steel be delivered as currently fabricated. To reduce the costs of rework that was inevitably required the as-built information was collected by default during their pre-install investigation scans providing them the data and knowledge from site to allow the revisions to be made by their internal drafting team and then the steel reworked in the workshop removing the inefficiencies from onsite fabrication and maintaining factory quality assurance processes are maintained.
The installation proved successful on the first go and rework costs kept to a minimum while providing their client with detailed rich reports of the issues found for their perusal with their 3rd party contractors for the identified defects.

Clash detections are found and minimized more quickly.
Clint also points out the fact that his team is now able to offer a better service to their clients in the form of maintenance and inspection on the reporting side. By having visual evidence in Cintoo, Studio Steel not only helps pre-design phases, but also leverages reporting to better monitor and maintain building structures. “Come to us with your problem,” Clint says, proving that Studio Steel can solve all problems whenever they occur in the lifecycle journey.