Scan to BIM for Energy Infrastructure: Turning Reality into Operational Intelligence
- Madeline Medensky
- July 14, 2025
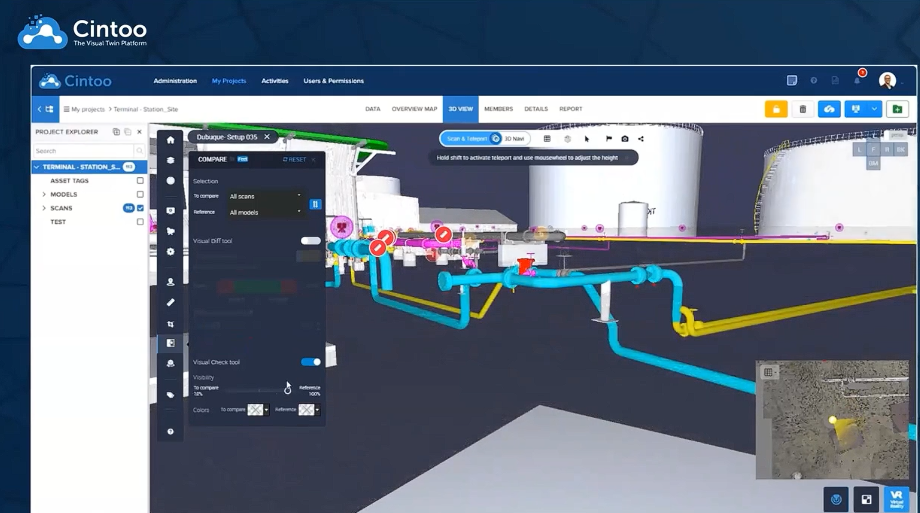
What is Scan to BIM for Energy Operations?
Scan to BIM for energy infrastructure refers to the process of converting high-resolution 3D scan data—collected from energy assets such as refineries, offshore platforms, gas processing plants, and terminals—into detailed Building Information Models (BIM). These models represent not just physical geometry but also embed critical metadata, enabling more informed decisions across the design, maintenance, and operations lifecycle.
In high-risk, capital-intensive energy environments, the need for accurate digital representations is non-negotiable. Scan to BIM delivers these by capturing as-is conditions with millimeter precision through terrestrial laser scanners, SLAM mapping, and drone-based photogrammetry. Once processed, the point cloud data is modeled into intelligent BIM elements such as pipes, structural supports, valves, and equipment units. These models are then used for retrofits, predictive maintenance planning, P&ID validation, and even regulatory audit support.
Unlike design-intent BIM models, which are often idealized and static, Scan to BIM reflects the true as-built condition—irregularities and all. This as-is accuracy is critical for energy companies operating facilities built over multiple decades, often without unified documentation or traceability.
What Types of Environments is This Important For?
Scan to BIM for energy infrastructure is vital in environments where spatial constraints, safety risks, and asset density demand meticulous planning and continuous oversight. These include upstream offshore platforms, where limited space and high operating pressure necessitate precise modeling for clash detection during brownfield modifications. Midstream environments, such as pipeline terminals and compression stations, benefit from Scan to BIM by reducing spatial uncertainty and ensuring accurate tie-ins for new piping or control systems.
Downstream facilities like refineries and petrochemical plants rely on Scan to BIM for accurate heat exchanger modeling, cable tray routing, and structural steel retrofits. Utility corridors in such facilities are often so dense that traditional measurement methods can’t deliver the fidelity required for re-engineering. Additionally, facilities undergoing digital twin adoption or IoT integration use BIM models as the backbone for overlaying real-time data from sensors, further justifying the need for scan-accurate geometry.
Tools to Use in the Scan to BIM Process
Scan to BIM begins with 3D data acquisition using lidar scanners capable of sub-centimeter accuracy. From there, platforms like Cintoo are used to process, visualize, and segment the data, allowing for the uploading and maangement of all scan data, regardless of its source.
Cintoo’s platform enables cloud-based point cloud-to-mesh conversion with TurboMesh, supporting seamless streaming and model navigation in browser-based environments. Once the mesh is validated and sectioned into zones or work packages, BIM authoring tools such as Autodesk Revit or Bentley OpenBuildings are used to create parametric models. Integration with ISO-compliant asset tagging systems ensures that each BIM element is not just spatially accurate but also enriched with metadata such as equipment ID, service type, or maintenance priority.
For QA/QC, platforms like Cintoo enable scan-to-model comparisons where geometric deviation is measured and reported automatically. This is critical in detecting misalignments between the scanned environment and proposed models, ensuring clash-free implementation during shutdowns or revamp projects.
BP Case Study: Scan to BIM in Operational Context
During a recent project, BP used Scan to BIM workflows to document and manage facilities across geographies. Laser scans were captured across multiple zones during routine maintenance, covering structural steel, piping systems, and mechanical rooms. Once the scan data was uploaded to Cintoo, it was segmented into operational zones.
From there, modelers converted the scan data into BIM components in Revit, including pressure vessels, pumps, pipe spools, and walkways. These BIM models were used in multiple downstream processes. First, they enabled virtual walkdowns for planning future shutdowns and assessing risks. Second, they served as the geometry base for adding live operational data—including pressure readings and valve positions—effectively transforming the BIM into a dynamic digital twin.
Cintoo’s scan-to-BIM deviation analysis played a pivotal role in QA. BP engineering teams used it to validate fabrication tolerances for skid-mounted equipment during pre-installation checks. By comparing the BIM model of the skid with the actual scanned environment, misalignment was detected in anchor bolt placement—preventing a costly on-site rework.
Beyond project execution, BP embedded the BIM models into its asset management systems, enabling field engineers to access 3D contextual views during inspections. This integration reduced planning time for corrective actions and supported real-time decision-making on high-consequence assets.
Potential ROI
The ROI from implementing Scan to BIM for energy infrastructure is multi-dimensional. One of the most direct benefits is rework avoidance. In the BP case, the detection of an alignment issue before skid installation saved tens of thousands of dollars in mobilization and rework costs. Scaled across a portfolio of assets, these savings multiply quickly.
Productivity gains also drive ROI. Digital walkdowns performed on scan-derived BIM models eliminate the need for repeat field visits—cutting planning cycles from weeks to days.
From a compliance standpoint, BIM models enriched with scan data support audit traceability, reducing time spent compiling documentation and improving regulator confidence. On the safety front, accurate models contribute to better risk assessments, scaffolding design, and confined space management.
Scan to BIM also supports faster handover to operations after capital projects. Instead of receiving redlines and outdated CADs, operators receive an up-to-date, navigable 3D model complete with metadata and asset identifiers. The model is thus more accurate since modelled from real-world, accurate conditions. This improves long-term maintenance planning and enhances institutional knowledge retention in an era of workforce transition.
Conclusion
Scan to BIM for energy infrastructure is far more than a documentation exercise—it is a transformation of how facilities are designed, operated, and maintained. From laser scanning to model generation, from asset tagging to operational integration, this workflow turns static infrastructure into dynamic insight.
Cintoo make this process scalable, secure, and efficient—bridging the gap between raw scan data and actionable BIM/CAD. As energy companies look to increase uptime, reduce risk, and modernize asset intelligence, Scan to BIM emerges as an essential tool in the digital transformation toolbox, reducing errors associated with miscalculated design work.
To learn how Scan to BIM can accelerate your project outcomes and improve operational intelligence, try a demo with a Cintoo expert today.