Why Turnaround Time is a Pain for Energy Operators: How Actionable Scan Data Can Help
- Madeline Medensky
- July 8, 2025
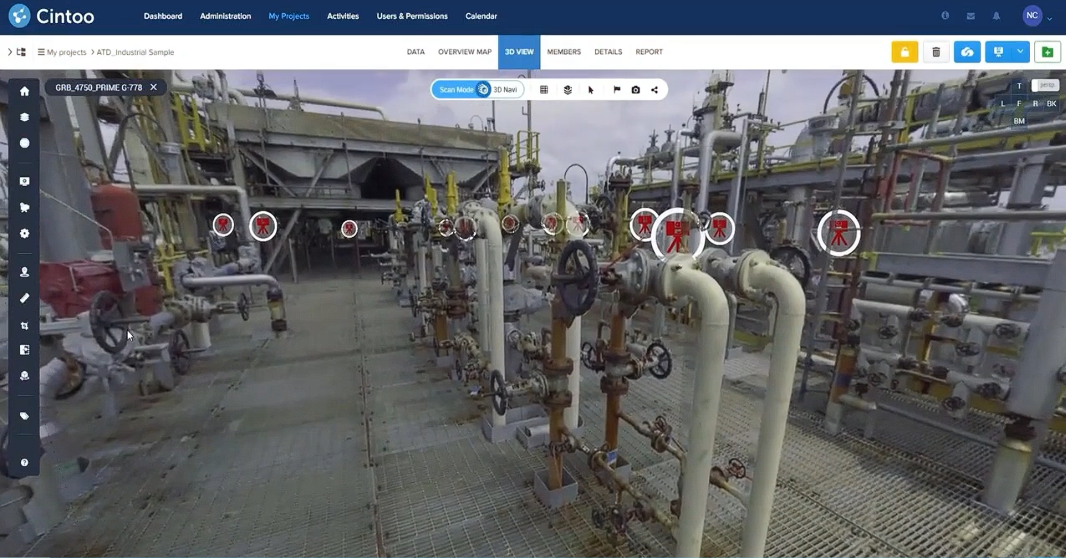
Why Turnaround Time Is a Pain for Energy Operators
In the offshore energy sector, few processes are as critical—or as costly—as turnarounds. These planned shutdowns for maintenance, inspection, and upgrades are necessary to keep operations safe and compliant, but they also come with steep consequences: every day offline can mean hundreds of thousands of dollars in lost production. For many operators, turnaround time (TA) is a race against the clock, complicated by tight budgets, complex logistics, and the pressure to deliver everything right the first time.
Unfortunately, traditional approaches to turnaround planning and execution often fall short. Manual walkdowns, outdated documentation, and siloed communication create delays, rework, and safety risks. Teams may spend weeks or even months preparing, only to encounter avoidable conflicts, scope creep, or inaccuracies once boots hit the ground. The cost of these inefficiencies adds up quickly.
The Challenge with Manual Workflows and Fragmented Teams
At the core of the problem is an overreliance on manual data collection and paper-based processes. Engineers and planners often travel to offshore sites multiple times to verify measurements, assess conditions, or develop work packages. These field visits are expensive, time-consuming, and frequently expose personnel to hazardous environments.
Compounding the issue is the poor quality—or complete absence—of up-to-date as-built documentation. Operators are forced to work from 2D drawings or outdated models that no longer reflect current field conditions. The result? Prefabricated components that don’t fit, miscommunications between departments, and workflows that grind to a halt midstream.
Even collaboration becomes a challenge. Static drawings, screenshots, or lengthy reports are passed between departments with little context, leaving room for misinterpretation. Teams working in siloes often don’t realize they’re out of sync until they’re already on site and behind schedule.
Laser Scanning and Reality Capture as a Turning Point
Laser scanning offers a way out of these pain points. By capturing precise, millimeter-accurate 3D representations of a facility, scanning enables operators to create a reliable digital model of their assets. It’s no longer necessary to make repeat site visits just to take a measurement. With a scan in hand, engineers can virtually “walk” the facility, plan modifications, and identify hazards from anywhere in the world.
This shift from physical to digital not only improves accuracy but dramatically reduces the need for travel, minimizes exposure to risk, and accelerates key stages of the turnaround process. Fabricators can cut parts to exact specifications using real-world data, contractors can evaluate space constraints before arriving onsite, and safety planners can conduct HAZOP reviews remotely.
In short, laser scanning replaces guesswork with clarity.
Going Further with Cintoo: Making Scan Data Actionable
However, scanning alone isn’t enough. Raw point clouds are notoriously difficult to manage—they’re large, complex, and require powerful desktop software to view and interpret. Without the right platform, scan data often becomes another isolated file, cut off from integration into workflows.
Cintoo transforms how scan data is stored, accessed, and shared. By converting point clouds into lightweight, high-resolution 3D meshes, Cintoo makes detailed scans viewable through any web browser—no special software, licenses, or high-end computers required. What was once accessible to only a handful of technical users becomes a collaborative tool for everyone involved in a TA project.
Cintoo’s platform isn’t just about visualization. It integrates with engineering tools like CAD and BIM, and—crucially—with enterprise platforms like asset management systems and ERPs. This opens the door to automating even more of the TA process: linking scanned assets to their operational metadata, maintenance histories, and procurement workflows. By syncing scan data, you unlock smarter planning, more informed decision-making, and long-term efficiencies that extend well beyond the turnaround itself.
Streamlining Every Stage of Turnaround Planning
Using Cintoo, the entire turnaround lifecycle becomes more efficient and precise.
Before work begins, teams can use the platform to define and verify the project scope, identifying assets or areas that need attention based on actual site conditions. Instead of relying on outdated drawings, they work from a real-time visual of the facility.
Work packages benefit, too. Planners can embed snapshots or 3D links from the scan into their documentation, giving contractors and field supervisors a clear view of what to expect. This leads to better preparation and fewer surprises.
Design teams can overlay proposed models directly onto the scan, making clash detection straightforward and visual. It’s easy to see if a new valve will fit or if scaffolding will obstruct another asset—issues that would otherwise cause delays during execution.
Cintoo also plays a major role in safety planning. Teams can assess confined spaces, determine access routes, or plan scaffolding layouts without setting foot onsite. These virtual walkdowns reduce safety risks, cut down on permit requirements, and accelerate planning.
Once fabrication begins, the scan data ensures components are built to spec. Accurate dimensions mean less rework, faster installation, and smoother handoffs. After execution, updated scans can be captured and uploaded into the platform, forming the basis for as-built records or updated digital twins. This data supports QA/QC, post-project documentation, and future planning cycles.
And when linked with your asset registry or ERP system, Cintoo’s visual data can help track changes, schedule preventive maintenance, or even trigger procurement actions—tying your visual reality to your operational systems.
Quantifying the Value
The efficiency gains of scan-based turnarounds aren’t just anecdotal—they’re measurable. Operators using Cintoo have reported significant savings across key areas:
-
Travel reduction: $10,000–$50,000 per TA
-
Avoided rework: $100,000+
-
Downtime reduction: $250,000+ per day
-
Improved safety planning: $20,000–$100,000 in compliance-related costs
Total potential value: $500K to over $1M per major turnaround.
When this process is integrated with existing enterprise systems, those savings scale further.
Conclusion: Smarter Turnarounds Start with Smarter Data
Offshore energy operators face enormous pressure to execute turnarounds quickly, safely, and on budget. The old ways—manual walkdowns, fragmented teams, inaccurate drawings—can no longer keep up with the demands of modern operations. Laser scanning is the unlock, and with Cintoo, that data becomes not just accessible but transformative.
From planning through to post-execution, Cintoo enables teams to make faster decisions, reduce waste, and minimize downtime. And by integrating with asset management and ERP systems, you can connect your 3D scan data directly to your operational workflows—multiplying the value of every scan.
Join a Demo today to see how it's possible.