What Is Reality Capture for Pipeline Inspection?
- Madeline Medensky
- May 27, 2025
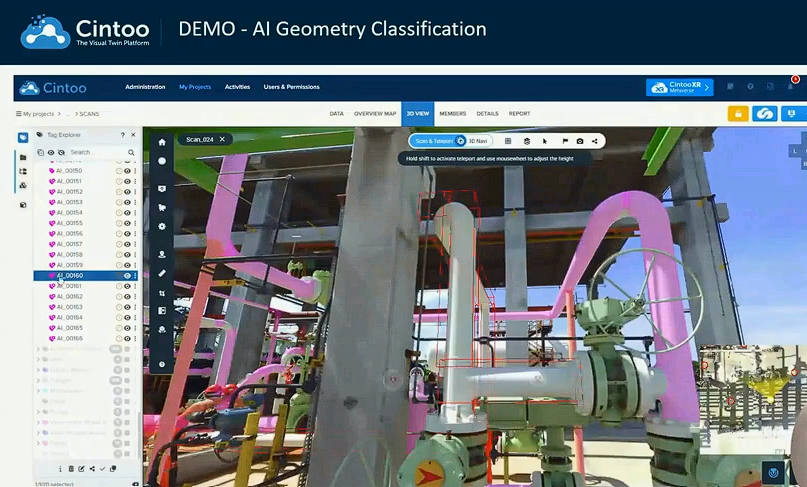
Reality Capture in the Context of Energy Operations
Reality capture refers to the process of digitally documenting real-world environments with high accuracy and fidelity using tools such as 3D laser scanning, drone-based photogrammetry, SLAM technology, and 360-degree imaging. In energy operations—where infrastructure is often vast, remote, and aging—reality capture has become indispensable for generating digital twins, supporting predictive maintenance, and enhancing asset visibility.
For pipeline inspection, reality capture technologies create a digital replica of field conditions by capturing millions of georeferenced data points across pipeline corridors, terminal facilities, valve stations, and pump sites. This data is then processed into point clouds and high-resolution meshes, forming the basis for engineering decisions, regulatory compliance, and remote collaboration. Unlike manual methods, which rely on field notes and delayed documentation, reality capture provides immediate, measurable insight into the physical state of critical infrastructure.
Role-Based Usage
Pipeline operators, maintenance managers, integrity engineers, asset owners, and HSE coordinators are key users of reality capture workflows. For these professionals, understanding the exact layout, geometry, and condition of assets—especially buried or partially obscured lines—is crucial to managing risk and scheduling repairs. In the context of integrity management, reality capture supports inspection planning, anomaly validation, and progress documentation for inline inspections (ILI), corrosion surveys, and hydrostatic testing.
HSE managers use the data to plan safe access routes and evaluate structural hazards in valve pits or access tunnels. Asset managers leverage reality capture to update GIS-linked registries and ensure that pipelines, flanges, valves, and instrumentation are all traceable and documented according to compliance requirements. As older engineers retire and institutional knowledge gaps grow, these digital datasets offer a durable, accessible visual reference for the next generation of technical staff.
Bringing Context to Pipelines
Pipelines are not only long and linear but are often co-located with other utilities, buried in inaccessible terrain, or passing through hazardous environments. Traditional surveys struggle to provide accurate, holistic visibility across such complex networks. Here, reality capture acts as a contextual bridge, providing rich spatial intelligence that can be used for everything from vegetation encroachment assessment to volumetric calculations of containment bunds. This reality capture data is then translated in point-cloud-to-mesh conversion on 3D scan data managment platforms, where it can be uploaded, viewed and managed.
The recent Neonex project—conducted for an energy operator with multiple terminal sites—demonstrated how 3D laser scanning and structured data management streamline pipeline documentation. Neonex deployed scanning teams across geographically dispersed terminals in Switzerland and Texas, capturing the condition and layout of both above-ground and buried assets. Using Cintoo, all collected data was uploaded to a central cloud platform where engineers could inspect mesh reconstructions, tag pipeline components, and align visual information with compliance documentation.
The value of this process lies in its immediacy and completeness. Engineers no longer need to rely on overlapping 2D drawings or out-of-date redline revisions. Instead, they are equipped with an interactive, multi-perspective model of the actual site. From flange dimensions and pipe diameters to isolation valve tagging and route access verification, the data offers unprecedented detail—all without stepping foot on site.
Performing Inspection from Reality Capture
Inspection teams using Cintoo gain access to powerful workflows for analyzing and comparing scan data over time. Once a laser scan of the pipeline corridor or terminal is captured and uploaded, users can isolate specific pipeline elements, zoom into buried connections, or perform deviation analyses against BIM models or previous scans. These scans are converted into high-resolution meshes using Cintoo’s TurboMesh technology, which enables cloud-based streaming without loss of accuracy.
Tagged assets, such as line breaks, drain valves, and pressure gauges, can be linked to metadata such as material grade, inspection status, corrosion rates, and installation dates. Annotated workflows allow engineering teams to flag anomalies directly in the 3D environment and share them in real time with stakeholders using platforms like Microsoft Teams. This drastically reduces the need for physical site visits and allows faster, more accurate inspection cycles.
Cintoo provides a suite of decision-maker tools tailored for multi-disciplinary teams. Asset managers can define and manage tagging schemas, run detailed queries against scan-linked asset databases, and export inspection results in structured formats for integration with other platforms. Project managers use Cintoo’s built-in measurement and sectioning tools to scope installation zones and visualize clearance requirements in tight piping corridors. Engineering leaders rely on the platform’s scan-to-model deviation analytics to ensure retrofit BIM/CAD designs are validated before execution.
Additionally, digital twin owners benefit from Cintoo’s change tracking and historical scan comparison tools, which allow users to visualize what has changed from one scan cycle to the next, providing a visual audit trail. These tools make reality capture not just a record-keeping system, but a living operational interface that bridges engineering, inspection, and executive oversight.
Cintoo also supports visual overlays from external sources, including Power BI dashboards and IoT sensors, enabling operators to correlate live operating data (e.g., flow rates, vibration metrics) with the physical geometry of the pipeline. For regulatory documentation, inspection results can be exported in CSV or integrated with CMMS systems to create traceable, time-stamped maintenance records. This level of integration elevates reality capture from a passive visual tool to an active element of decision-making.
Possible ROI
The return on investment from using reality capture for pipeline inspection can be measured in multiple dimensions. First, there is a substantial reduction in inspection costs. For example, in the Neonex case study, four terminal sites were scanned and documented in under four weeks—2.3 times faster than traditional methods. This not only accelerated P&ID development but also eliminated the need for repeat site visits, which typically incur travel, safety, and personnel costs.
Second, there is a quantifiable increase in inspection accuracy and scope. Laser scanning captures all visible elements in one pass, removing the risk of missing undocumented features like branch valves or buried sensors. With each scan archived in Cintoo, operators can perform change detection analysis, reducing the likelihood of unnoticed degradation or unrecorded modification.
Third, the reality capture approach significantly improves project scalability. In one Neonex example, more than 650 P&IDs were generated in under ten months by a distributed team of 40 CAD designers using Cintoo as their central data hub. Traditional methods would have taken up to five years. This increased throughput translates to faster compliance cycles, improved safety reviews, and reduced capex planning delays.
Finally, the use of cloud-native platforms like Cintoo enhances team collaboration and compliance transparency. Whether planning a reroute, conducting a HAZOP, or resolving a leak event, all stakeholders are working from the same source of truth.
Conclusion
Reality capture for pipeline inspection is no longer an emerging technology—it is an essential component of modern pipeline integrity management. With high-resolution scan data and robust platforms like Cintoo, energy companies can achieve a level of spatial clarity and operational intelligence that fundamentally transforms how pipelines are inspected, maintained, and documented. From reducing physical site exposure and accelerating design cycles to enhancing compliance and minimizing risk, reality capture delivers a measurable, strategic advantage. For next steps, watch a live demo from BP here.