3D Point Cloud Capture: How Planning Ahead Maximizes the Value of Your Scan Data
- Madeline Medensky
- July 16, 2025
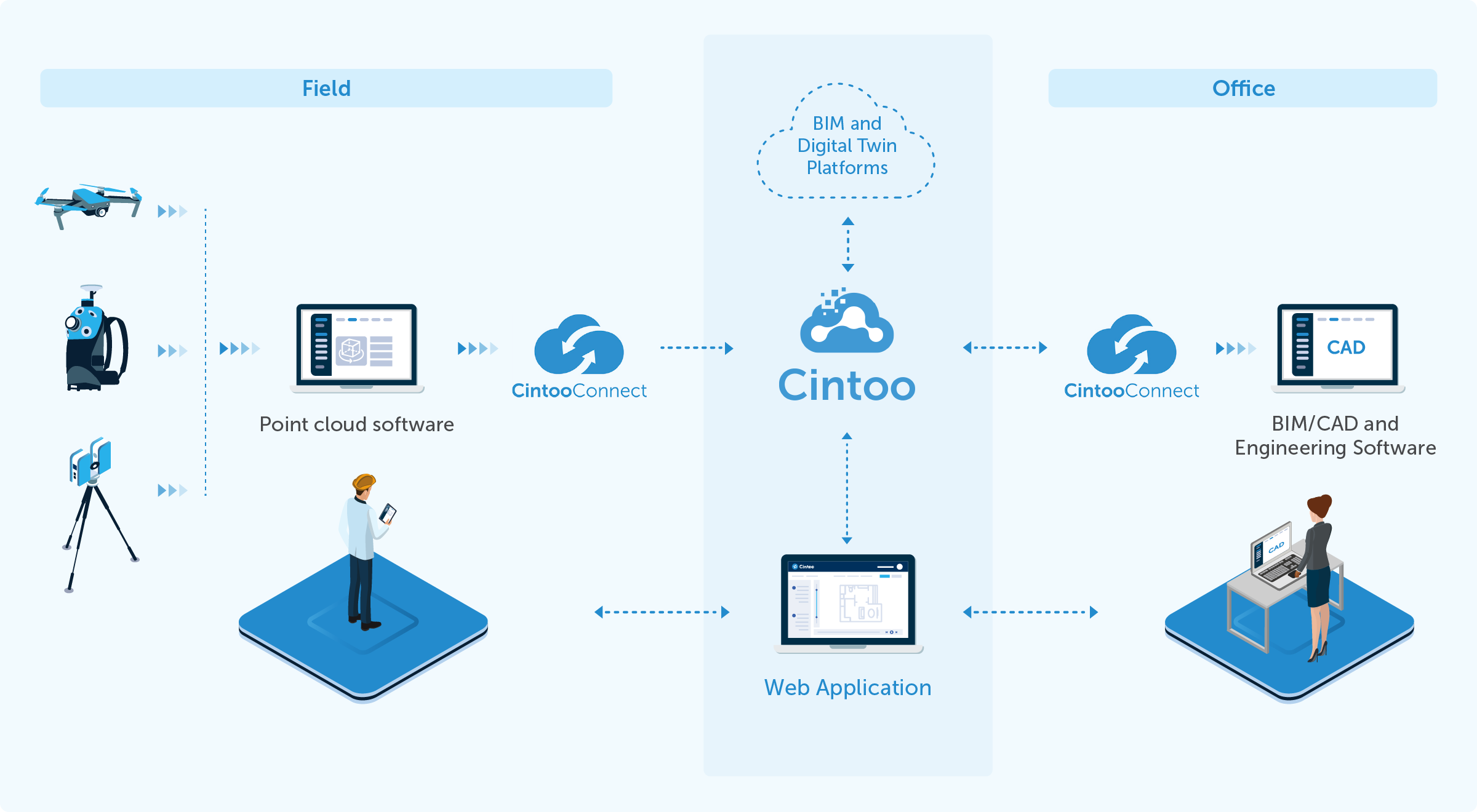
Project efficiency depends on accurate 3D point cloud capture, especially for downstream data usage. Whether you’re building a digital twin of an industrial plant, retrofitting legacy infrastructure, or validating as-builts against a BIM/CAD model, the quality and clarity of your point cloud data can either make or break the success of your project.
Capturing the best possible scan data doesn’t just come down to using the latest terrestrial laser scanner or drone. The secret lies in what happens before the scanner is even turned on. It starts at the planning stages, when project goals are set to determine how the data will be used afterwards.
Why Planning Is Essential to High-Quality 3D Point Cloud Capture
Most teams understand the benefits of laser scanning. It’s fast, non-intrusive, and offers a highly detailed representation of real-world conditions. However, many still dive into scan projects without a clearly defined purpose or understanding of downstream workflows.
This is where costly mistakes happen—gaps in data, misaligned coordinate systems, or poor resolution that renders the scan unusable for scan-to-BIM or asset management workflows.
By planning first and scanning smart, teams can define exactly what needs to be captured, who will use the data, and how it will support critical project milestones.
Step One: Define the Purpose of the Scan
Before any scanner hits the ground, ask: What is the primary goal of this scan?
Whether you’re capturing a facility for digital twin integration, simulating maintenance inspections, or validating design tolerances, understanding the objective upfront shapes every decision that follows—from which scanner to use to how the data is structured and tagged.
For example:
-
A scan supporting retrofit design must be captured at a resolution that meets model tolerances.
-
If the goal is regulatory compliance, high-fidelity data is needed to verify measurements against engineering specs.
-
For ongoing operations, assets must be clearly tagged and searchable within the 3D mesh.
Step Two: Involve Stakeholders Early
The value of 3D point cloud capture is best realized when all data users are considered at the outset. Engineers, project managers, safety inspectors, and operations staff all interact with the data differently.
Engaging these stakeholders during planning helps ensure:
-
The right scan resolution is used for each area.
-
The output format is compatible with downstream platforms (e.g., BIM, CAD, GIS).
The data supports remote access, virtual walk-throughs, and clash detection—all critical to modern digital workflows.
This cross-functional alignment transforms point cloud data into a strategic asset that can be used for downstream purposes.
Step Three: Match the Technology to the Job
One of the most common missteps in 3D scanning is using the wrong tool for the job. Site conditions vary widely, and choosing the appropriate laser scanning technology—whether terrestrial, mobile, or drone-based—is essential to capturing usable, accurate data.
Here’s a quick guide:
-
Terrestrial Laser Scanners (TLS): Best for indoor environments and high-detail work such as mechanical rooms or plant floors.
-
Mobile Scanners (SLAM): Ideal for fast scanning of corridors, large facilities, and areas with limited access.
-
Drone Scanning (UAV): Perfect for outdoor sites, roofs, or large campuses where aerial visibility adds value.
Each scanning method comes with tradeoffs in speed, resolution, and required control, but by understanding your goals and site constraints, you can select the right combination.
Step Four: Prep the Site and Build a Scanning Strategy
Site prep may seem minor, but it plays a massive role in scan quality. Reflective surfaces, moving equipment, temperature fluctuations, and tight access points can all impact data clarity. Conduct a walk-through to flag problem areas and plan scanner positions accordingly.
Key steps include:
-
Removing loose objects or reflective materials.
-
Defining safe scanner locations with adequate overlap (25–50% is ideal).
-
Placing survey targets or GPS markers for control and alignment.
-
Breaking the site into manageable scan zones for better organization.
Real-world example: When iScano documented a historic church in Toronto, they discovered undocumented spaces and difficult-to-reach areas. A modular scanning approach and structured zones helped the team adapt dynamically and collect a complete dataset of the site, taking their time to assess which areas needed new scanning techniques.
Step Five: Structure and Upload to the Cloud
Once the scan is complete, it’s time to transition from raw point cloud to actionable data. Using a cloud-based platform like Cintoo, your scan data is uploaded, structured, and converted into lightweight 3D meshes—retaining all the resolution of the original scans while enabling seamless navigation in the browser.
Cloud-native reality capture tools eliminate the hassle of local servers and hard drives while unlocking benefits like:
-
Real-time collaboration across global teams.
-
Virtual inspections without site visits.
-
Overlay of BIM or CAD models for comparison.
-
Versioned, centralized data management with one source of truth.
With Cintoo’s hardware-agnostic approach, data from any scanner—terrestrial, mobile, or drone—can coexist in the same environment.
Scan-First, Not Model-First
Many organizations still default to model-first strategies, only to realize too late that their digital representation doesn’t reflect the actual site. A scan-first approach flips this logic—capturing as-built reality from day one and building the model around it.
This has a direct impact on ROI. Starting with accurate, 3D point cloud capture can help set the stage for accurate understandings and precise coordination, saving companies time and money on projects given the elimination of rework or mistakes. Others have reduced site visits by half, accelerated retrofit timelines, and even avoided six-figure rework due to early clash detection.
Best Practices Summary
Here’s how to get the most out of your 3D point cloud capture project:
-
Plan before you scan. Know the end-use of your data and who will consume it.
-
Choose the right technology. Tailor scanning tools to site conditions and data needs.
-
Engage stakeholders early. Alignment across teams prevents data gaps and inefficiencies.
-
Prep your site. Identify hazards, constraints, and target placement in advance.
-
Use the cloud. Upload structured scans to enable collaboration, QA/QC, and advanced workflows.
-
Think scan-first. Let the reality of the site drive your digital twin strategy—not the other way around.
Final Thoughts
3D point cloud capture is a foundational element of the digital transformation sweeping across architecture, engineering, construction, and industry. But to realize its full potential, it must be approached strategically.
Planning your scan project with intention sets the stage for every success downstream. From seamless scan-to-BIM validation to collaborative digital twin development, the clarity of your point cloud depends on what you do before the first scan even begins.
If you're ready to scan smarter, reduce rework, and deliver higher-value data to your team, the first step is simple: plan first.
Want to see it in action?
Schedule a demo with Cintoo’s surveyor-trained team to learn how to streamline your 3D point cloud capture workflow and transform your scan data into a collaborative, cloud-ready asset.