From Scan to Reality: How to Use Progress Monitoring
- Madeline Medensky
- May 6, 2025
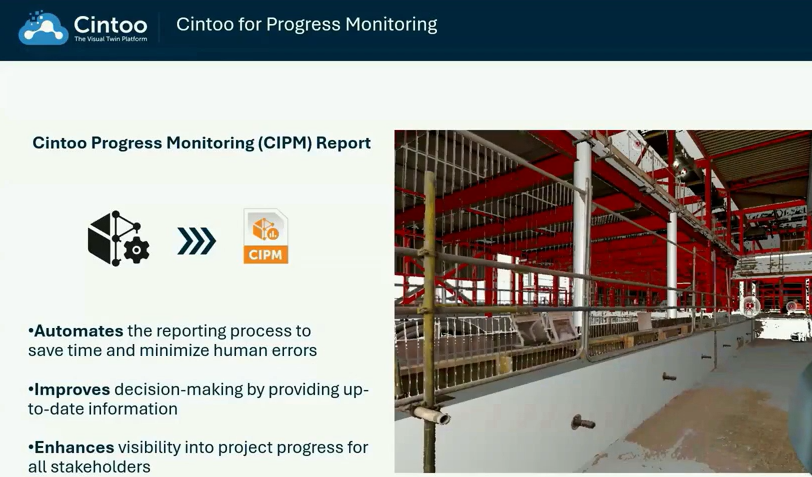
As construction projects grow in complexity and scale, so does the challenge of accurately tracking progress. For project owners, contractors, and architects alike, having a real-time pulse on how a site is evolving is no longer a luxury—it’s a necessity. Enter progress monitoring: a powerful technique that leverages 3D scan data and digital models to provide objective insights into construction development.
This blog explores what progress monitoring is, why it’s crucial for the construction industry, and how Cintoo is transforming this workflow with an automated, data-driven approach.
What is Progress Monitoring?
In the context of the AEC (Architecture, Engineering, and Construction) industry, progress monitoring refers to the process of comparing 3D scan data captured on-site with the corresponding digital model, such as a BIM (Building Information Model). By overlaying reality capture data with design intent, stakeholders gain an objective understanding of what has been built, what has not, and how closely construction aligns with specifications.
Unlike manual inspections or 2D drawings, this method reduces guesswork, increases traceability, and enables digital documentation. Cintoo’s progress monitoring workflow enables users to run comparisons between laser scans and model elements, then generate CSV reports that quantify percentage coverage and distance deviations for precise insight into project status.
How Does Progress Monitoring Impact the Construction Industry?
The implications of progress monitoring extend across the construction lifecycle. First, it enhances quality control by detecting construction deviations to within millimeters, allowing issues to be identified and addressed early. Second, it reduces rework, which can be one of the most expensive outcomes of late-stage discovery. By validating each construction stage against the design model, teams can avoid costly corrections.
Progress monitoring also improves stakeholder communication. Clear, quantifiable visuals and reports ensure that everyone—from field engineers to owners—is aligned with the actual progress and conditions on-site. In addition, it supports data-driven scheduling. Project managers can easily identify whether structural elements or MEP installations are ahead of or behind schedule and adjust workflows accordingly.
Finally, progress monitoring creates legal and contractual evidence. Timestamped reports validate claims of completed work and support dispute resolution when needed. Studies indicate that integrating laser scanning into construction workflows can reduce rework by up to 50 percent and produce ROI of three to five times the original investment by mitigating delays and reducing material waste.
3D Scan Data and Cintoo’s Offering
At the heart of Cintoo’s progress monitoring is a straightforward yet powerful concept: digitize the as-built condition and compare it to the design model inside a centralized, web-based environment.
Cintoo allows automated comparisons between 3D scan data and BIM models such as those from Revit, IFC, or NWD formats. Users can define specific distance thresholds—measured in millimeters or inches—to identify acceptable tolerances. They can isolate particular elements, such as structural steel or mechanical systems, to analyze their construction progress in detail.
The results of these comparisons are stored in CIPM files, which can be exported as CSV spreadsheets. Each report contains model element names and IDs, percentage of coverage by scan data, and maximum, average, and minimum distances from model elements to actual as-built conditions. This level of granularity supports informed decision-making and simplifies reporting.
The workflow begins with visualizing scans within a designated work zone using Cintoo’s 3D viewer. Next, users select model elements they wish to analyze from the model explorer. Once the model-to-scan tolerance is set, the tool runs in the background, and users receive an email once the report is ready for download. Element IDs can then be cross-referenced in the 3D viewer to investigate deviations or gaps in construction.
Cintoo supports both terrestrial and SLAM-based scan data and offers compatibility with various file types, including OBJ meshes and Navisworks formats. This ensures adaptability across different project scales and scopes.
Case Study: Comparing Scans Over Time
Consider a real-world scenario involving a mid-rise commercial project. In July 2024, the site was scanned using a terrestrial laser scanner. A structural Revit model containing steel columns and framing was also uploaded to the platform. When the first progress monitoring report was run, several model elements displayed zero percent coverage, indicating they had not yet been built.
Project teams used the CSV report to identify specific element IDs corresponding to these unbuilt components. Those IDs were pasted into the viewer to locate and verify their absence visually. This immediate feedback loop allowed for quick alignment between project expectations and on-site reality.
A second scan captured in August 2024 showed additional construction progress. A new monitoring report showed updated coverage percentages and revised deviation metrics, confirming the construction of previously unbuilt elements. The ability to compare scans across time periods provided a visual and quantitative timeline of development.
Progress monitoring is reshaping how construction teams plan, execute, and verify their work. By replacing subjective evaluations with precision scan-to-model comparisons, organizations reduce risk, streamline workflows, and deliver greater accountability. Cintoo enables fast, repeatable progress assessments through an intuitive interface that supports a variety of scanning methods and file types.
Teams can generate clear and actionable reports, integrate seamlessly with BIM environments, and support broader workflows such as QA/QC, scheduling, and historical documentation. Whether tracking weekly milestones or verifying subcontractor performance, Cintoo empowers construction professionals to maintain clarity and confidence at every stage of the build.